Jan Berbee became "infected with the packaging virus" during his career. As a sustainable packaging consultant, he helped companies reduce their use of tape, plastic and boxes. Until he came across a mushroom farmer who was looking for an alternative to the blue plastic containers. Says Berbee, "That's when I discovered mushroom packaging."
Credit: Grown.bio
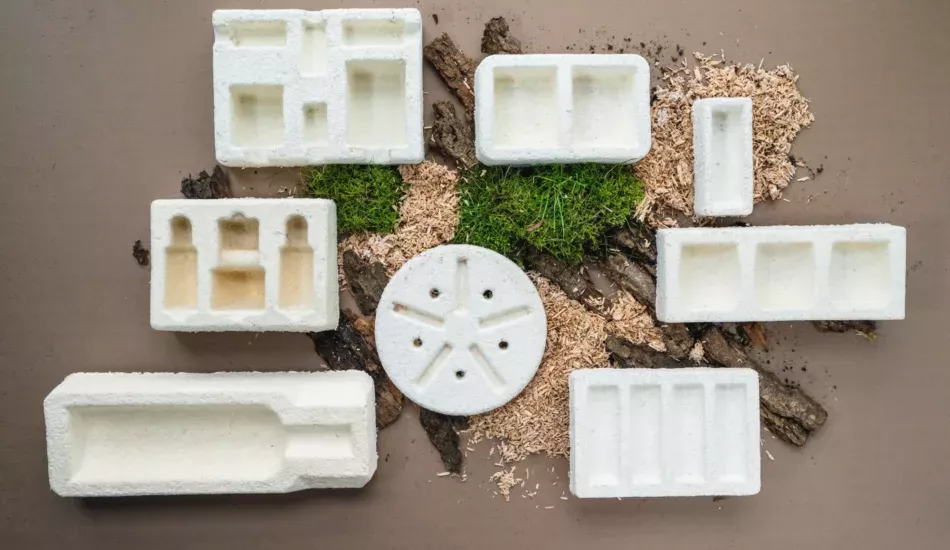
First, let's go back to school. Under the cap of a mushroom are spores. Those spores can become detached and end up in the soil via the wind. Such a spore starts secreting enzymes in the form of threads that grow into the soil. The result is a network of fungi that can cover an area of several square kilometers. That network of fungal threads is called mycelium. You could write a book about the wonderful world of mycelium in nature (or watch the Netflix documentary Fantastic Fungi).
Mycelium packaging
Berbee became enchanted when he heard that two American students were using mycelium for packaging, as an alternative to Styrofoam. "They already had patents, so we went right into licensing negotiations," he says. Not long after, Berbee founded his own mycelium company, Grown.bio. "A few months later, we were able to start growing mycelium in the shed at my house."
Molds and fungi
.Mycelium growing works as follows: "You start by designing a packaging mold on the computer," Berbee says. "From that shape you make a plastic mold. We do that from recycled PET. You then fill the mold with substrate. That's a mixture of mycelium and fibrous agricultural residues, which the mycelium feeds on. In five to six days, under a temperature of 25 degrees, the substrate grows to the shape of the mold. After that, you have a living mold in the shape of the package. This mold is still 50 percent water. In the last step of the process, we put the mold in the oven under a temperature of 80 degrees. This kills the mold, stops its growth and evaporates the water. The result is a cured biobased packaging mold."
A large part of the work, then, is in waiting for the mold to grow. "On Fridays we fill the molds. Tuesdays we do a quick check to make sure no strange things are happening, and on Thursdays we come back to put the molds in the oven."
Rest streams from agriculture
.According to Berbee, there are many advantages to packaging made of mycelium, in addition to being a petroleum-free material as a replacement for Styrofoam. "In addition to mycelium, the substrate consists of agricultural residues. For example, we use hemp from Groningen or straw from rabbit pens. In Spain we managed to use chaff from paella rice as food for the fungus. And we have done the same thing with the cutting waste from a champagne house."
Also, the mold is not flammable, its insulation values are good and the packaging is to some extent moisture resistant. "For example, we also have a project where our packaging is used in the fish industry," Berbee says. "In the packaging goes fish, ice and water. That stays good for at least a week, long enough for the duration of transport."
Compostable pen container
.And after use, the mycelium packaging simply composts in nature. "In the winter months it takes six to seven weeks, just in my own garden. In the summer when it's warmer and more humid, it goes a little faster. Also, the packaging can go with the flow of paper recycling." But actually Berbee prefers to see higher-quality applications, where the packaging remains whole. "Like a pencil case or as a compostable flower pot."
Biobased building
The versatile benefits of mycelium also make the material suitable for use in construction, such as for wall panels and insulation. Yet Grown.bio recently decided to focus only on packaging materials. "Primarily because we can make a huge impact if we eliminate Styrofoam from the world. Of course, the construction industry is huge. But the downside is that in every country there are different certifications that construction materials have to meet. And the process of certification is time-consuming and costly. But construction, especially for the future, remains an interesting market."
New factory
.In the coming years, Berbee hopes to make Grown.bio bigger. Now his factory still produces 300,000 packages a year. But he already has plans for a new factory with a capacity of 10 million to open in 2025. For that, he is still looking for investors. "The nicest thing is if this is a strategic financier, someone who knows the packaging industry well."
Packaging for white goods
."For now, we are focusing mainly on the luxury segment, such as perfumes and champagne," Berbee continues. "Our packaging material is four times more expensive than Styrofoam. So that's especially interesting for customers who believe in our story, have sustainability ambitions themselves and have budget to invest extra in packaging. We can really make big hits if we can serve large white goods manufacturers. Those volumes are huge. We now have one such customer. But a process like this - from testing to production - takes a long time."
Level playing field
.But the market for mycelium will only really take off if politicians manage to create a level playing field for biobased materials over fossil-sourced packaging. "Ultimately, business is driven by profit, so politics must intervene. If the CO2 price of plastics is factored in, the prices could level out. Fortunately, there are also positive developments. We get subsidies and pay virtually no waste management fee compared to plastics. And France is already coming up with a ban on single-use Styrofoam."
If Berbee can dream? "Then by 2030 we will have five mycelium factories scattered throughout Europe. Where the mycelium in the substrates will be fed with local agricultural residue. The concept lends itself fantastically to local entrepreneurship."
Source: change.inc