Turning discarded materials back into high-quality products. That is the essence of a circular economy. But that is far from easy, as recent bankruptcies in the plastic recycling industry show. Yet it is not all misery. AVK Plastics has been making new products from recycled plastic for decades and, with the help of two other companies in the chain, will soon be able to process even more material.
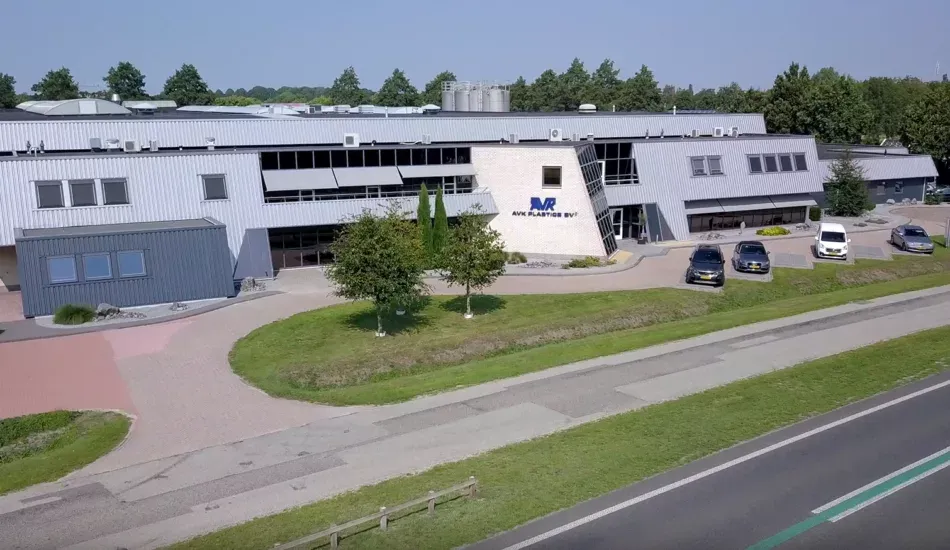
"We are a bit of an odd man out," says Arno Kanters, director of AVK Plastics. "As part of the Danish AVK Group - which mainly produces metal valves - AVK Plastics focuses precisely on plastic products." The company founded in the Netherlands and now active throughout Europe, makes products such as street pots, transport pallets and mobile waste containers from recycled plastic with the lowest possible environmental impact "We only add new additives to our recycled plastic in small amounts, such as for coloring products or better processing. But the starting point is that the final product is also fully recyclable again."
Recycle beverage cartons
.AVK Plastics has been working with Recon Polymers since 2022. This Roosendaal-based company processes PolyAl waste from beverage cartons into reusable raw materials for the plastics industry. PolyAl is the residue of plastic and aluminum that remains after paper mills extract paper fibers from used beverage cartons. Tetra Pak, producer of beverage cartons and food processing solutions, invested another €1 million in Recon Polymers' recycling technology by 2023. Those investments are important because advanced technology is needed to process the PolyAl residual stream in such a way that it yields a raw material that AVK Plastics can use for new products. The capital injection increases recycling capacity to at least 8,000 tons per year. This will allow about 30 percent of PolyAl from beverage cartons to be recycled in France, Belgium and the Netherlands.
Clean grain
."It's important that we get a recycled pellet that meets the right specifications so we can do something with it," Kanters says. "We can then blend this grain up to about 20 percent into our recipe for new products." These are made by AVK Plastics through injection molding. The plastic recipe is heated and melted with an injection molding machine and pressed into a cooled steel mold. When the plastic has cooled and solidified sufficiently, the mold is opened and a new product made of recycled plastic remains.
The injection molding process is finely tuned; if the recipe changes, the process often has to be adjusted as well. Kanters: "The PolyAl granulate that we receive through Recon, we can currently only process in the recipe for transport pallets. That is the first application we have addressed. But in the future, I also see opportunities for some of our other products."
Technical Innovations
.AVK Plastics has been working with recycled plastics since its inception and has seen its production volumes grow steadily. "So we also need more and more volume of raw material," Kanters says. "So working with partners who can offer us a stable and consistent material flow is essential. The cooperation with Recon Polymers and other partners such as Tetra Pak is ideal because we can work with them openly and transparently, enabling us to implement technical innovations faster."
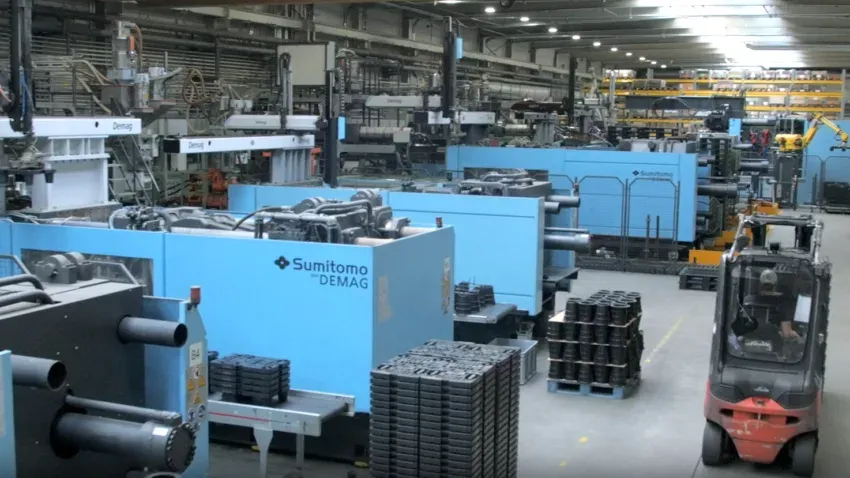
Facilities
The market for recycled plastic has changed. Whereas recycled material used to be considered inferior, it is now increasingly in demand. Yet in recent months, several leading plastic recyclers have gone bankrupt, such as Umincorp and Ioniqa. The reason according to these companies: cheap virgin plastic from abroad and lagging policy measures, such as the blending requirement for plastic recyclate in new products.
But Kanters does not think that such an obligation alone is going to sort out a desirable situation. "For some companies, the mandatory switch to recycled material is going to be difficult because they are used to the predictable properties of new plastic. Their processes are geared to that. We have quite a large engineering department that focuses precisely on this kind of challenge."
Addition requirement
Didn't companies then have plenty of time to get their production processes ready for the 2027 blending obligation? "The regulations fall short on an entirely different problem, namely ensuring that enough clean, usable recycled plastic is available," Kanters said. "If companies will soon be required to use 30 percent recyclate, they will have to look for recyclate with the properties of virgin material. That may be possible for some waste streams. But if you want recycled plastic with the properties of virgin, you still end up with a very expensive secondary material. I fear that there will soon be far too little recyclate available, while the demand for plastics will only continue to rise."
Burning less
.Love Kanters sees measures that ensure more plastic is recovered from waste. For this, more effort should be put into collection, sorting and processing. "A ban on burning plastic waste would be a step in the right direction. Ideally, regulations would ensure that waste ends up at recyclers rather than incinerators. Such an approach would improve the availability of recycled raw materials and help companies make their products more sustainable."
Source: change.inc