It sounds like a recipe for a compelling entrepreneurial story: a now-deceased inventor who turned out to be ahead of his time and developed a unique recycling technique in his garage in the 1990s. Two former classmates who meet again after 30 years and start a business. And a partnership with food giant Unilever to ensure that thousands of tons of plastic will soon be recycled. The story of OBBOTEC has it all.
Head of technology Diederik Jaspers (l) and Wouter van Neerbos, director of OBBOTEC (r). | Credit: OBBOTEC
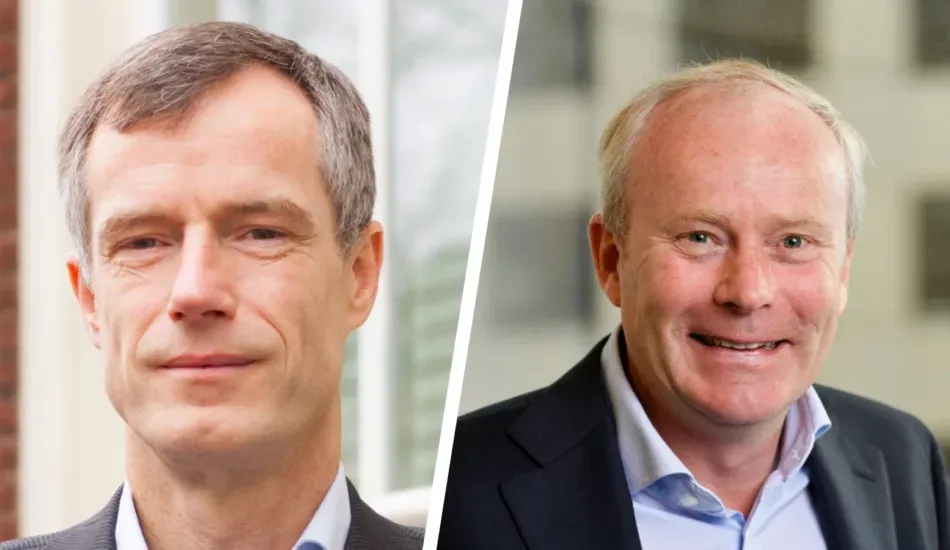
Change Inc. is invited to Plant One in the Botlek, Rotterdam's industrial area west of the Old Meuse River. Apart from Chemelot in Geleen, it is the only place in the Netherlands where start-ups and scale-ups are permitted by permit to test pilot plants in the petrochemical playing field. Passing giant installations, steaming chimneys and multiple entrance gates, we are led through a large factory hall past various companies active in recycling and petrochemicals. This included Ioniqa, declared bankrupt in October, where it is logically somberly quiet at the moment. It is anything but quiet in the part of the plant where OBBOTEC is located. A team of operators has been busy all week performing tests with a brand new installation that most resembles a gigantic church organ. The goal: to turn old chip bags, shampoo bottles and other plastic packaging into new clean plastic.
Leonardo Da Vinci
The story of OBBOTEC begins somewhere in Obbo Hazewinkel's garage, says Diederik Jaspers, the company's chief technology officer. "Obbo was a serial inventor, a kind of Leonardo da Vinci," Jaspers says. "He invented a technique to solve the manure problem, developed technology for making fuel from waste and is the creator of the dissolution recycling technique that we are building on now." Jaspers ran with Hazewinkel in his researcher years. "He was the master, I was the apprentice."
Lamentably, Obbo Hazewinkel died in 2014 and saw none of his innovations reach full maturity. His ideas ended up on the shelf. But in the years that followed, the circular economy received more and more attention and the need for innovation increased. So in 2018, son Sander Hazewinkel, together with Diederik Jaspers and Wouter van Neerbos - who still knew each other from high school - decided to dust off Obbo's ideas and bring them to market. OBBOTEC was born.
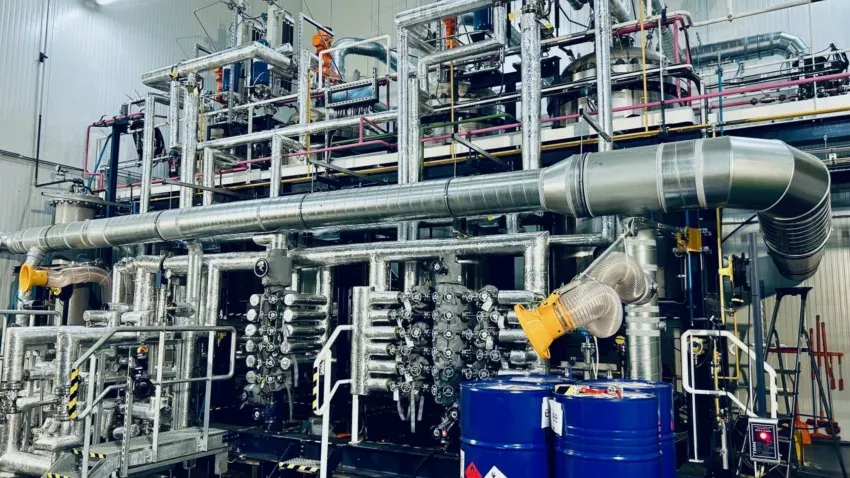
Technology
OBBOTEC's technology, called SPEX (Selective Plastic Extraction), focuses on recycling different combinations of plastic streams, such as HDPE, LDPE and PP. To do so, it uses a technique based on dissolution, or dissolving and purifying plastics under pressure with a special solvent. "The beauty of our technology is that we can extract different polyolefins from a waste stream, including from waste streams consisting of mixed plastics and aluminum," explains Wouter van Neerbos, director of OBBOTEC. "With our solvent, we extract all additives down to the molecular level from the plastic waste, such as flame retardants, fragrances and dyes." OBBOTEC then separates the solvent back from the dissolved plastic. With already existing techniques, the purified polymers can be made into plastic pellets again. Virtually no loss of material occurs during this process. "What remains are white, odorless plastic flakes that are just as clean as virgin plastics."
Part of OBBOTEC's secret is in the composition of the chemical solvent, which the company can use over and over again. The rest of the magic is in timing the heating, filtering and cooling of the feedstock. That happens in the complex tubing system visible at the front of the pilot plant, controlled by software the company developed. OBBOTEC says its dissolution technology sits between that of mechanical and chemical recycling. But unlike mechanical recycling, dissolution results in much higher quality material, while being much less energy intensive and giving higher yields than chemical recycling. Van Neerbos: "We had an LCA (Life Cycle Assessment, ed.) of our technique carried out by CE Delft. Because of the high yield and high quality that we realize, we come out considerably better than mechanical or chemical recycling."
Cooperation with Unilever
.But a promising technology alone does not make a profitable business. Building large plants costs millions, and OBBOTEC needs a guarantee that the recycled plastic will find a market. For that, the company is counting on food giant Unilever, among others. Unilever is closely involved in OBBOTEC's development and is in the Rotterdam Circular project with the company. Where OBBOTEC was able to test and improve the SPEX technology, Unilever provided packaging to run the pilots with, knowledge about detailed quality and legal requirements, and introductions to the wide network of raw materials and packaging.
At an event discussing the European Plastic Pact, Van Neerbos got talking to Unilever's Thor Tummers. "The event was a consultancy paradise," recalls Tummers. "A lot of talking, little doing. After I met Wouter, we actually explored pretty quickly how we could work together. That's kind of the Rotterdam mentality after all."
Food grade
This cooperation with Unilever focuses on two sides of the recycling process: on the one hand, the processing of complex plastic packaging via the SPEX technology, and on the other, the application of high-quality recycled material in new packaging. Here, a major milestone would be reached if OBBOTEC's recycled material is allowed to be applied in new food packaging. Indeed, OBBOTEC may demand a higher price for recycled plastic suitable for food packaging. That type of plastic is now scarce. That way, the company can compete with virgin material.
But current laws and regulations do not allow the recyclate to be used in food packaging for the time being. Food packaging is now made from virgin plastic or material derived from chemical recycling. But OBBOTEC claims their recyclate is even cleaner than virgin plastic because the material is also stripped down to the molecular level of contaminants sometimes found in petroleum.
Legal not technical
"The bar is high for new technologies like ours," says Van Neerbos. "The challenge of making food grade packaging from recycled materials is more legal, rather than technical." At the same time, Van Neerbos and Tummers see that policy is slowly moving in the right direction. Tummers: "We are in talks with the Ministries of Infrastructure & Water Management and Health, Welfare & Sport to adjust European rules and procedures. And we also see that the Dutch Food and Consumer Product Safety Authority is closely involved to suggest improvements. Normally such a process takes seven years. We want to do it in four years. And parties like Mars and PepsiCo are also hooked up in the FlexForward project with Wageningen University. For us, these developments are not exclusive. We will benefit if competitors also think this is a good idea, so that the scale can become much larger."
Other bankruptcies
.OBBOTEC, meanwhile, is in a market that has been struggling in recent months. After Umincorp in January and TRH Recycling in July, Ioniqa - which has a test site at Plant One - also collapsed in October. The reason: cheap virgin plastic from abroad and failing policies. Van Neerbos does make it clear right away that the bankruptcies of other plastic recyclers are not one-to-one comparisons. "But the threat of cheap fossil plastic from China is not going away," he says. "And the moment new factories come along that start making plastic from fossil raw materials with enormous capacity, nobody is going to be happy. The beauty is precisely that we can avoid that fossil route, and high-quality recyclate is scarce. But the business case has to come out."
Future plans
.There is no shortage of ambition in any case. The Rotterdam plant is currently capable of reprocessing waste batches of 100 to 200 kilograms into clean material within a few hours. Ultimately, OBBOTEC hopes to open a site capable of processing 25 kilotons per year as early as 2027. Van Neerbos: "For this, involvement of Verpact (the organization responsible for packaging collection and recycling, ed.) is important, to make suitable materials available in the development and scaling up of our technology."
After 2027, OBBOTEC plans to build similar plants throughout Europe. Where these factories will be located is not yet known. But near a packaging manufacturer would be a logical choice, says Van Neerbos. "So that literally a discarded shampoo bottle goes in at one end, and a new, fully recycled variant comes out at the back."
Source: Change Inc.